Portable Hydraulic Mule
Operator-Height Hydraulic Command Post – Hydraulic controls are at elbow-height, for comfortable and efficient operation over a long work day. Compare to other brands with crucial controls low to the ground, making the operator lean over to operate basic mill functions. Full-Time Hydraulic Control. Crucial hydraulic log-handling tools. Portable Hydraulic Mule Kit Designed for DEPENDABILITY and PERFORMANCE. Assembled Typical 6 GPM Mule Kit with reservoir, pump motor starter, filters, and shut off valves. Portable Hydraulic Mules; Customize; Sign up; Log in; Copy shortlink; Report this content; Manage subscriptions.
Hydraulic Ground Power Unit – Hydraulic power units, sometimes called a hydraulic mule, provide hydraulic pressure to operate the aircraft systems during maintenance. They can be used to:
• Drain the aircraft hydraulic systems.
• Filter the aircraft system hydraulic fluid.
• Refill the aircraft system with clean fluid.
• Check the aircraft hydraulic systems for operation
and leaks.
Manufactured in many sizes and cost ranges, some have a limited range of operation, while others can be used to perform all the system tests that fixed shop test stands are designed to perform.This type of portable hydraulic test unit is usually an electrically powered unit. It uses a hydraulic system capable of delivering a variable volume of fluid from zero to approximately 24 gallons per minute at variable pressures up to 3,000 psi.
Operating at pressures of 3,000 psi or more, extreme caution must be used when operating hydraulic power units. At 3,000 psi, a small stream from a leak can cut like a sharp knife. Therefore, inspect lines used with the system for cuts, frays, or any other damage, and keep them free of kinks and twists. When not in use, hydraulic power unit lines should be stored (preferably wound on a reel) and kept clean, dry, and free of contaminants.
What are Hydraulic Power Units?
Hydraulic power units (sometimes referred to as a hydraulic power pack) is a self-contained system that generally includes a motor, a fluid reservoir, and a pump. It works to apply the hydraulic pressure needed to drive motors, cylinders, and other complementary parts of a given hydraulic system.
How Does a Hydraulic Power Pack Work?
A hydraulic system employs enclosed fluid to transfer energy from one source to another, and subsequently create rotary motion, linear motion, or force. The power unit/pack provide the power needed for this transfer of fluid. Rick ross trilla album zip.
Unlike standard pumps, hydraulic power units use multi-stage pressurization networks to move fluid, and they often incorporate temperature control devices. The mechanical characteristics and specifications of a hydraulic power unit dictate the type of projects for which it can be effective.
Some of the important factors that influence a hydraulic power unit’s performance are pressure limits, power capacity, and reservoir volume. In addition, its physical characteristics, including size, power supply, and pumping strength are also significant considerations. To better understand the operating principles and design features in a hydraulic power unit, it may be helpful to look at the basic components of a standard model used in industrial hydraulic systems.
Hydraulic Power Pack/Unit Design Components
A large, durable hydraulic power unit built for functioning under a range of environmental conditions will have numerous design characteristics distinct from a typical pumping system. Some of the standard design features include:
- Accumulators: These are containers that can be attached to the hydraulic actuators. They collect water from the pumping mechanism and are intended to build and maintain fluid pressure to supplement the motor pumping system.
- Motor Pumps: A hydraulic power unit can be equipped with a single motor pump, or multiple devices each with their own accumulator valve. With a multiple pump system, usually only one operates at a time.
- Tanks: The tank is a storage unit designed with enough volume for the fluid in the pipes to drain into it. Likewise, actuator fluid may sometimes need draining into the tank.
- Filters: A filter is typically installed along the top of the tank. It is a self-contained bypass unit, with its own motor, pump, and filtering apparatus. It can be used to fill or empty the tank by activating a multi-directional valve. Because they are self-contained, filters can often be replaced while the power unit is functioning.
- Coolers and Heaters: As part of the temperature regulation process, an air cooler can be installed near or behind the filter unit to prevent temperatures from rising above operational parameters. Likewise, a heating system, such as an oil-based heater, can be used to elevate temperatures when necessary.
- Power Unit Controllers: The hydraulic controller unit is the operator interface containing power switches, displays, and monitoring features. It is necessary for installing and integrating a power unit into a hydraulic systems, and can usually be found wired into the power unit.
How to Select Hydraulic Power Motors
The power source, or prime mover, associated with most hydraulic power units is the motor, which is generally selected based on its speed, torque level, and power capacity. A motor whose size and capabilities complement those of the hydraulic power unit can minimize wasted energy and raise cost-efficiency in the long-term.
The criteria for motor selection vary according to the type of power source being employed. For example, an electric motor has an initial torque much greater than its operating torque, but diesel and gasoline-powered motors have a more even torque-to-speed curve, delivering a relatively steady amount of torque at both high and low running speeds. Consequently, an internal combustion engine may be able to initiate a loaded pump, but not provide enough power to bring it to operating speed if it is not properly matched with the hydraulic power unit.
Motor Size
As a rule of thumb, the power rating for a diesel or gasoline motor used with a hydraulic power unit needs to be at least double that of an electric motor suitable for the same system. However, the cost of the electricity consumed by an electric motor over its operational lifespan usually outstrips the cost of the motor itself, making it important to find an appropriately sized unit that will not waste energy consumption. If the pumping pressure and liquid flow are set at a constant rate, motor size can be measured according to the following parameters:
• Horsepower
• Gallons per minute
• Pressure, measured in pounds per square inch (psi)
• Mechanical pumping efficiency
In some cases, the hydraulic system may require different levels of pressure at various stages of the pumping process, meaning that horsepower can be calculated as the root mean square (rms) and a smaller motor may suffice for the project. However, the motor must still be able to meet the torque requirement for the highest pressure level in the cycle. Once the rms and the maximum torque (including initial and operational levels) have been calculated, they can be cross-referenced with a motor manufacturer’s performance charts to determine whether the motor is the necessary size.
Electric Motor Power
Electric motors and internal combustion motors, such as diesel or gasoline engines, exhibit different torque characteristics that dictate their varying power capacities. A typical three-phase electric motor begins its operating sequence by turning a rotor. When the rotor accelerates, the torque level drops slightly, then increases again when the rotation hits a specific rpm rate. This temporary drop is known as “pull-up torque,” while the maximum value is designated as “breakdown torque.” When the rotor speed surpasses the breakdown level, torque decreases steeply. An electric motor’s torque-to-speed curve remains roughly the same regardless of power capacity, and it is usually run at full-load speed but below the breakdown point to reduce any risk of stalling.
Gasoline and Diesel Motor Power
Internal combustion motors have a significantly different torque-to-speed curve with fewer torque fluctuations. Generally, diesel and gasoline motors have to operate at higher speeds to achieve the necessary torque to power a pump. A horsepower rating approximately two and a half times greater than that of an electric motor counterpart is typically required for an internal combustion engine to reach the torque levels needed for a hydraulic power unit. Manufacturers normally recommend that gasoline or diesel motors operate continuously at only a portion of their maximum rated power in order to prolong the motor’s lifespan, and keeping the torque below maximum level can often improve fuel efficiency.
Operating Process of Hydraulic Power Units
Used Aircraft Hydraulic Mule

When a hydraulic power unit begins functioning, the gear pump pulls hydraulic fluid out of the tank and moves it into an accumulator. This process continues until the pressure within the accumulator reaches a predetermined level, at which point a charging valve switches the pumping action to begin circulating fluid. This causes the pump to release fluid through a charging valve back into the tank at minimal pressure. A special one-way valve keeps fluid from flowing out of the accumulator, but if the pressure drops by a significant amount, the charging valve reactivates and the accumulator is refilled with fluid. Farther down the line, a reduced-pressure valve regulates the flow of oil moving to the actuators.
If the accumulator is equipped with a fast-stroking device, it can be connected to other accumulators to allow them to charge pressure as well. Often, an automatic thermostat or fan will be included to help alleviate rising temperatures. If the fluid in the system begins to overheat, a temperature switch can shut the motor-pump off, which can also help refill the tank if its fluid level is too low. If the hydraulic power unit has multiple motor pumps, a flow switch can have them alternate in case of reduced fluid supply. Pressure switches can be used to regulate accumulator pressure and a monitoring system can alert operators when pressure has dropped too low, elevating the risk of power unit failure.
Other Hydraulic Articles
More from Electrical & Power Generation
Portable Hydraulic Metal Shear
Thomas Industry Update
Stay up to date on industry news and trends, product announcements and the latest innovations.
Related Resources
Portable Hydraulic Mule
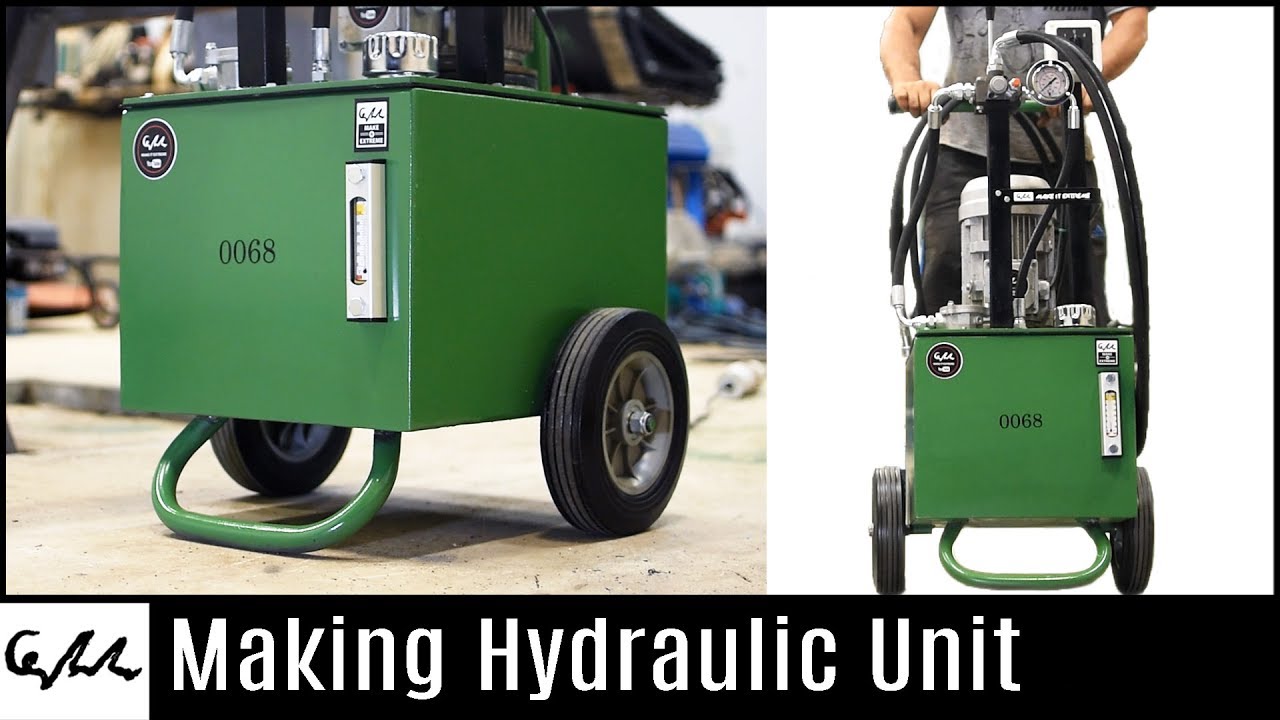

Aircraft Hydraulic Mule For Sale
Reducing, Reusing, Recycling, 1 Item at a Time
SupplyOne Acquires Florida Packaging Supplier
Baltimore Steel Manufacturer Acquires Nation's Largest Wire Handles Producer
7 Industry Updates You Need to Know This Week [60-second Read]
Receiving $10.5 Million in Federal Funding, Alabama Linen Manufacturer to Open PPE Plant
Browse by Category
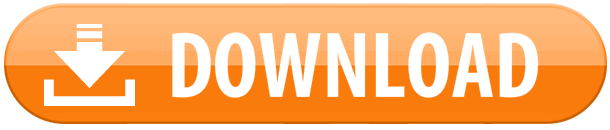