Heat Input Formula Kj Mm
- Heat Input Formula Kj Mm Conversion Chart
- Heat Input Formula Kj/mm
- Heat Input Formula Kj Mm Squared
- Welding Heat Input Formula Kj/mm
Heat input is an important variable in welding, with standards or specifications often placing restrictions on the variation in heat input between a PQR and a WPS. There are a range of approaches to this, which are summarised in the below:
EN ISO 15614-1: Where hardness requirements apply, the lower limit of heat input qualified is 25% lower than that using in welding the test piece. Where impact requirements apply, the upper limit of heat input qualified is 25% greater than that used in welding the test piece.
Heat Input kJ/mm (kJ/in) Or Remarks 1 to 3 SMAW E7018 4.0 mm (5/32) 160-200 24-26 N/A 5-10 (in/min) Root Pass 4 to n SMAW E7018 4.8 mm (3/16) 220-250 24-26 N/A 5-10. The enrgy input, Qin, can be defined as: Qin = HHV fuel. m f,actual. Two separate fuels can be tested to observe the changes in engine performance with the Engine Performance Applet with Fuel Type. This applet also includes the effect of heat transfer using Woschni's correlation.
ASME IX: Heat input is a supplementary variable, applicable when notch-toughness tests are specified. The WPS specified heat input may not be greater than that recorded on the PQR (not including overlay applications). Heat input can be measured directly, or alternatively, the heat input may be determined by volume of weld metal deposited (per unit length of weld). This volume may also not be greater than that recorded on the PQR.
ASME IX Interpretation IX-81-19 stated that the maximum heat input that should be determined from a PQR is based on the combination of maximum current and voltage with minimum travel speed. It is not based on an average of the heat input of all of the passes. Interpretation IX-04-14 further clarified that the combination of parameters to determine maximum heat input must all come from the same pass or unit length of weld.
Heat Input Formula Kj Mm Conversion Chart
AWS B2.1: This takes the same approach as ASME IX, with the WPS heat input not being greater than that recorded on the PQR where toughness requirements are specified.
AWS D1.1: Again, heat input is a supplementary variable for toughness applications. How to talk to man hussey pdf files. However, D1.1 also contains limits on each electrical parameter, placing limits on the current, voltage and travel speed (with some variation between process). So D1.1 is potentially slightly more rigorous in terms of heat input.
AWS D1.5: This is the most explicit standard in terms of specifying how heat input should be controlled. It provides methods of testing for maximum or minimum heat input or both, along with restrictions on the variation allowed in heat input during PQR testing. Specifically, it states that the heat input of all weld passes (excluding root and cap) should be within +-10% of the average heat input of all of those passes. This requires post-test calculation and then retesting as required. There are also further limits on the heat input range that is allowed on the WPS relative to the PQR
As you can see, there is limited guidance or consensus on how to control and analyse heat input when performing welding procedures with multiple passes. ASME IX explicitly allows a very wide heat input range for a WPS or PQR, whereas AWS D1.5 places tight controls on it. This situation can result in significant disagreements between customers and suppliers who might have different viewpoints regarding how acceptable this is. This makes it important to specify up front how this issue is to be resolved.
If design, application or client codes don’t precisely specify how this data is to be processed, there are three common approaches that can be taken.

1) Weld two test pieces, one at a low heat input and one at a high heat input. Test both. Consider everything between the two to be qualified. While you could make the argument to use the lowest heat argument from the first and the highest heat input from the second, it’s more reasonable to use the average heat input from each weld.
2) Use the highest heat input recorded during the PQR plus the specified tolerance and the lowest heat input minus the specified tolerance as the limits. This is the widest possible and will make welding within the limits easier. It may have an impact on quality.
3) Weld a single test piece, and specify variations based on the average heat input recorded, such as one standard deviation (SD) or a % above and below the mean value. The tolerances can then be placed on this processed data, either the mean or the mean +- one standard deviation.
4) Weld a single test piece, and place requirements on the heat input variation allowed within that test piece. This might be either a specified +-%, as in AWS D1.5, or a value based on the heat input recorded, such as one standard deviation (SD) above and below the mean value. The tolerances can then be placed on this processed data, either the mean or the mean +-one standard deviation.
For all of these approaches, it’s important to consider that for multi-stage welds (eg TIG root and FCAW fill and cap), the different stages must be considered and controlled separately.
To demonstrate the variation these approaches can generate, it’s worth looking at an example set of data, from a theoretical PQR, using MIG welding, in the table below. (Note, I'm not including a thermal efficiency factor of 0.8. here, so assume it's as per ASME IX.)
Current (A) | Voltage (V) | Travel speed (mm/s) | Heat input (kJ/mm) |
214 | 21.9 | 5.03 | 0.93 |
217 | 21.9 | 4.86 | 0.98 |
212 | 21.8 | 3.83 | 1.21 |
213 | 21.9 | 3.96 | 1.18 |
214 | 21.9 | 5.08 | 0.92 |
212 | 21.9 | 4.48 | 1.04 |
211 | 21.6 | 4.69 | 0.97 |
191 | 22.3 | 3.83 | 1.11 |
For this set of data, we've got a mean heat input of 1.04 kJ/mm. We can now process this data in a range of ways, to provide a range of heat inputs for the WPS. These are shown in the table below, from least to most stringent. (Here, % is % of the mean value.)
Min HI (kJ/mm) | Method | Max HI (kJ/mm) |
0.66 | Min to Max ± 25% | 1.47 |
0.78 | Mean ± 25% | 1.3 |
0.84 | Mean ± 1 SD ± 10% | 1.27 |
0.92 | Min to Max | 1.21 |
0.93 | Mean ± 1 SD | 1.15 |
0.94 | Mean ± 10% | 1.14 |
All of these methods of calculating a WPS heat input range are valid (unless otherwise specified by code), but exactly which is picked can significantly vary weld quality and ease of welding. It should be considered prior to any sort of multi-pass weld qualification.
The Collie Welding Heat Input Calculator will calculate these possible ranges for a set of user data.
(Found this page useful? If so, please consider making any planned purchases through these links to Amazon UK or Amazon US to support Collie Welding at no cost to yourself.)
This article provides information about ASME Section IX Heat Input Calculation and qualification range. The heat input is supplementary essential variable in the most welding process, it means if the construction code e.g. ASME Code Section VIII is not requiring the impact testing, then heat input will be nonessential variable.
Heat Input Formula Kj/mm
When minimum design metal temperature and thickness combination required impact testing, then heat input matters. In this case, the heat input must be calculated based on following formula, and your WPS must be re-qualified (new PQR) if there is an increase in your heat input for new job:
Heat Input = [(Voltage x Amperage) x 60]/ Travel Speed
if your travel speed unit is inch/ min then your heat input unit will be J/inch
If your WPS is qualified with Hard facing overlay or corrosion resistance overlay, then 10 % increase in the heat input will be nonessential variable but more than 10% increase in the heat input will be essential variable.
Example for ASME Section IX Heat Input Calculation
For instance if you welding process is Gas Tungsten Arc Welding (GTAW) and your voltage is 15 V and your amperage is 100 A, and the welder travel speed is 5 inch/min then the heat input will be
Heat Input = (15 x 100)x60/ 5 = 18000 J/inch
Mariah carey bye bye remix mp3. So if you have any job that you need higher heat input above 18000 J/inch, then you need to requalify your WPS, but if this is about hard-facing overlay or corrosion resistance overlay process, then this heat input can be increased up to 19800 J/inch ( 10 % of 18000) without WPS requalification.
Heat Input Formula Kj Mm Squared
The ASME Section IX Training Course is 2 days video training course and available online and the student that successfully pass the exam, receive I4I academy certificate with 16 hours training credit.
Did you find this article useful? Click on below Like and G+1 buttons!
Welding Heat Input Formula Kj/mm
New! Comments
Have your say about what you just read! Leave me a comment in the box below.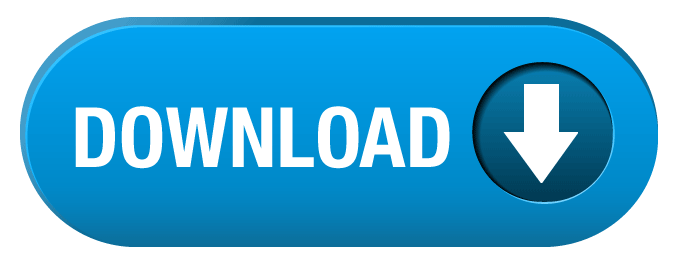